Mistakes that Cause Frontline Workers to Resist Adopting Digital Quality Inspection Management
Implementing a digital quality inspection system can revolutionize a manufacturing organization’s approach to maintaining high-quality standards. It offers real-time insights, enhanced data accuracy, and boosts productivity for both quality and production teams. However, the success of digital quality control hinges on its adoption by frontline workers—the people who will use it daily.
Unfortunately, there is a common disconnect between the needs that drive projects and the outcomes when digitalizing frontline processes as highlighted by research done by Deloitte and Forrester. The need for frontline digitalization is great, with only 23% of frontline workers stating they have the technology they require to be productive. However, almost 70% of digitalization project failures are due to poor user adoption, especially for frontline digitalization projects.
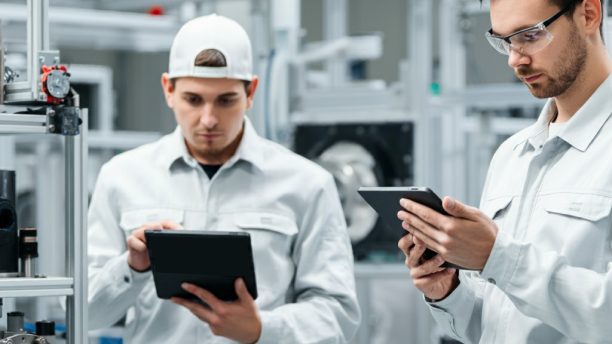
With digital quality control projects, it is critical to emphasize how frontline workers will interact with the system and its impact on their typical flow of work. For the most part, digital systems are designed for office workers, with text-heavy digital forms and checklists that are not intuitive for frontline workers. Several common issues arise from these office-centric interfaces and related implementation practices that can undermine adoption and lead to frustration, inefficiency, and, ultimately, the system’s failure.
Poor Usability & Complex Data Entry
A system that is difficult to navigate or requires cumbersome data entry can quickly become a source of frustration for its users. Poor usability directly affects workers’ efficiency and accuracy, slowing down inspections, increasing the likelihood of mistakes, and ultimately causing workers to abandon the system altogether. If workers feel the system is making their jobs harder, their frustration will likely lead them to revert to manual methods, undermining the benefits of the digital system.
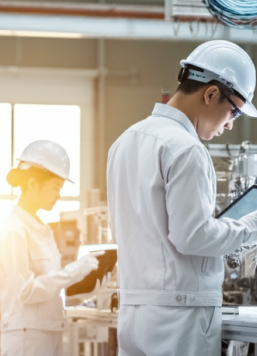
Solution: To avoid this pitfall, prioritize user-friendly design during the selection of the digital technology, and the design and implementation of the system. The interface should be clean, simple, and easy to navigate, even for those who may not be tech-savvy. Data entry processes should be streamlined with features like drop-down menus, multi-choice or multi-select answers, autofill options, and error-checking prompts to reduce the burden on workers and ensure data accuracy.
Lack of Personalization
Another common mistake when implementing a digital quality inspection system is taking a one-size-fits-all approach. Different organizational roles have different needs; the same applies to workers with differing experience levels. A system that does not allow for personalization adds barriers to adoption and consistency of use. Experienced workers will want the fastest, fewest clicks possible, whereas new workers may need more detailed guidance to ensure proper adherence to the process and accurate data capture.
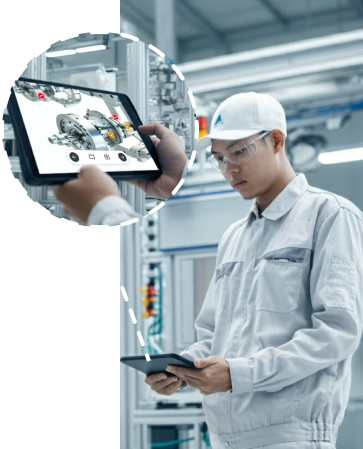
Solution: Ensure that the digital quality inspection system offers role and team specific configuration options. Workers should be guided directly to the inspections, equipment and workflows that are relevant to their job. Look for technology that allows workers to set their own customized views of information within the system. Design options into the inspections for training and in-process guidance that allow experienced workers the ability to access guidance only when they need it. Some advanced platforms can also deliver customized workflows based on user roles or experience levels to ensure that frontline workers…
Download the comprehensive PDF report to continue reading and explore actionable strategies for adopting digital quality systems.