Introduction to the Connected Worker
Digital tools have transformed our daily lives, from ordering food to managing finances. But industries like manufacturing have yet to fully embrace digital connectivity for their frontline workers. Many workers still rely on manual data collection on clipboards, paper-based work instructions, and a hoge-poge of communication methods.
The emergence of easier, smarter digital technologies is changing that. Today’s frontline digital technologies are going beyond extending a mobile interface to corporate systems, they are guiding and assisting workers to improve performance and productivity. The era of the connected worker has arrived.
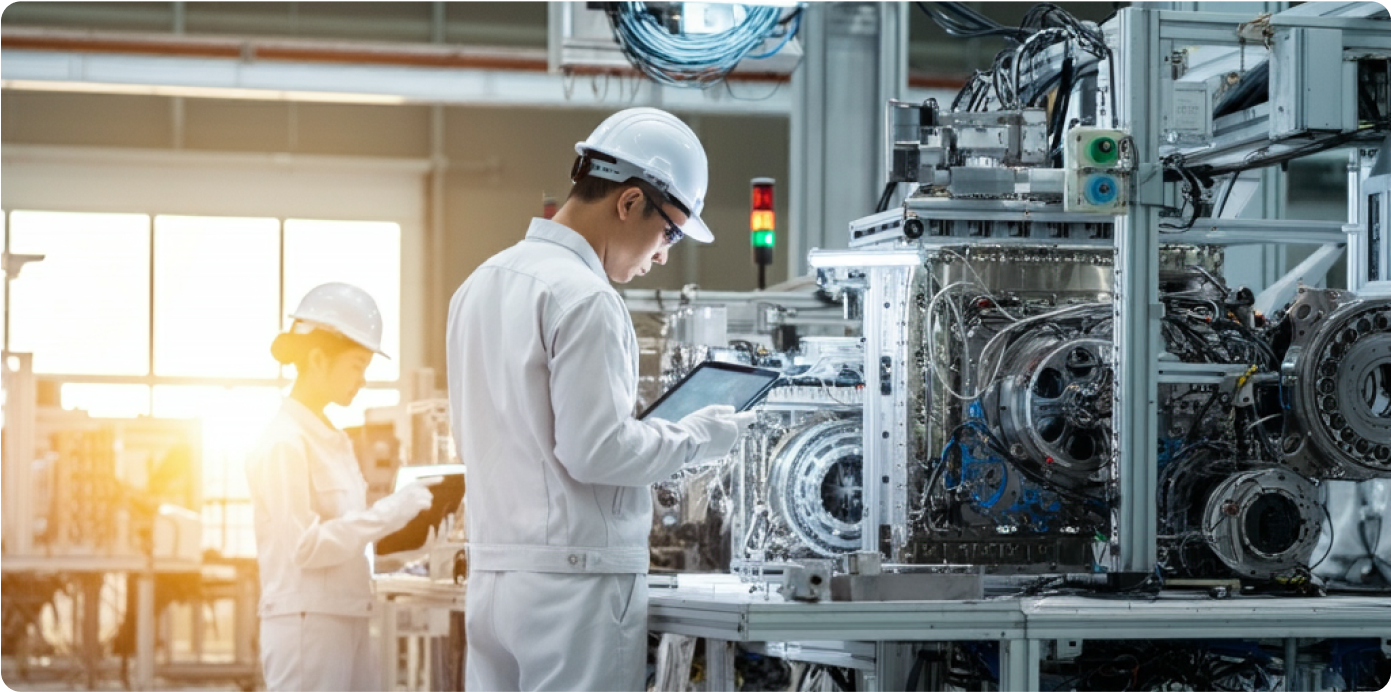
Connected worker solutions bridge the gap between the workforce and the data that drives operations, making frontline workers more efficient, informed, and empowered. These technologies create a seamless flow of information, improving safety, accuracy, and productivity.
What You'll Learn in This Guide
This guide will provide insights into:
- The concept of the connected worker
- Different types of connected worker technologies
- The benefits of connected worker technologies
- Key use cases and real-world applications
- How to choose the right connected worker solution for your organization
By the end, you’ll have the knowledge and tools to implement connected worker solutions and drive transformation in your operations.
What is a Connected Worker?
The concept of a connected worker is the empowerment of frontline employees with digital tools that accelerate onboarding and skills attainment, enhance safety, boost performance and productivity, and improve real-time decision-making. These tools actively exchange data with machines, devices, and management systems, embedding workers into a responsive, digitalized ecosystem that enhances collaboration across the company.
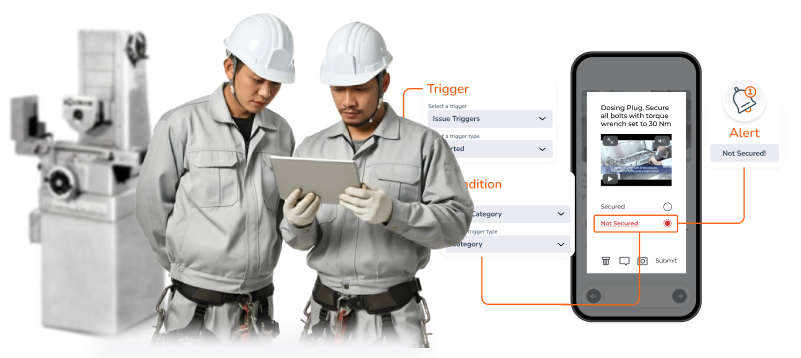
Connected worker technologies are varied and include purpose-specific solutions that can integrate a broad set of hardware and software solutions, such as:
- Mobile applications
- AI-powered digital assistance
- Wearable devices
- Augmented reality (AR) tools
- Industrial Internet of Things (IIoT) sensors
- Collaboration and messaging tools
By embedding workers within intelligent, data-driven systems, organizations can enhance efficiency, reduce errors, and create safer, smarter workplaces.
Benefits of Connected Worker Technology
Connected workers benefit manufacturing, field service, and industrial operations.
Key advantages include:
Faster onboarding
Engaging, interactive content and on-the-spot training build worker skills more quickly.
Improved Safety and Compliance
Reduce risk and facilitate hazard reporting through connectivity and compliance tracking
Better Decision-Making
Real-time data ensures workers make informed choices, reducing errors.
Operational Visibility
Gain a clear view of every production stage and instant access to issues and resolutions.
Standardized Process
Easily accessed digital SOPs ensure consistency across experience levels, teams and sites.
Lifelong Learning and Skill Development
Simplify access to training and engage workers and managers in collaborative skills development.
Enhanced Communication and Collaboration
Make it easier for workers and teams to seek assistance and share knowledge.
Reduced Data Errors
Automated systems simplify data collection and prevent mistakes in data entry.
Increased Efficiency
Faster access to information reduces non-productive time and streamlines work processes.
Increased Equipment Reliability
Ensure consistent maintenance and leverage predictive intelligence to reduce unplanned downtime.
Data-Driven Insights
Digitally capture frontline activity and data to enhance existing information systems.
Want to calculate
the business impact?
Digitizing frontline operations boosts revenue and cuts costs. Studies show 15-30% higher labor productivity, 25-30% lower maintenance costs, and 30-50% less equipment downtime. Try our business impact assessment tool for insights.
Connected Worker in Manufacturing
The manufacturing industry faces a dual challenge: significant labor shortages and a widening skills gap. Despite efforts to rehire many of the 1.4 million workers laid off during the pandemic, manufacturing companies are struggling to fill roles, with many reporting high turnover and challenges in retaining new hires.
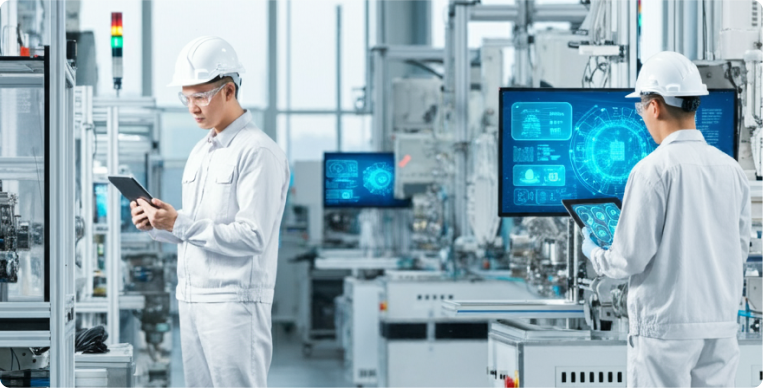
Addressing the Skills Gap
The skills gap in manufacturing is amplified by both the retirement of experienced workers and the increasing complexity of advanced manufacturing equipment and processes. Additionally, younger generations of workers expect digital-friendly workplaces to assist them with daily tasks. Connected worker solutions bridge this gap by:
- Accelerating onboarding of new hires
- Delivering on-the-spot work guidance
- Fostering skills development with on-demand training
- Automating repetitive data collection tasks
- Providing easier, faster communication and collaboration
- Enabling a safer workplace through real-time alerts
Targets For Connected Worker Solutions
Connected worker technologies benefit all levels of an organization, from the factory floor to the executive suite.
-
Production Technicians
Digital work instruction and improved communications and collaboration. -
Quality Control
More consistent inspection with automated data collection and real-time visibility to issues and trends. -
Equipment Operators
Faster, easier setup and maintenance, improved compliance to preventive maintenance schedules. -
Field Technicians
Digitalized inspections and data capture with easier access to documentation and remote support. -
Safety Teams
Simplify safety notices and reporting, and enable faster response and corrective action. -
Mechanics
Deliver more effective issue data with images and video to ensure faster response and first-time fix. -
Engineers
Gain real-time visibility into production data, enabling data-driven process improvements. -
Executives
Access to live operational dashboards to drive informed decisions that lead to improved performance.
What is a Connected Worker Platform?
A connected worker platform is a digital solution with a variety of integrated capabilities designed to equip frontline workers with the real-time information and instructions they need to improve performance, safety and quality. These platforms streamline work processes, improve communication, and boost overall productivity by leveraging digital tools to connect, automate, and visualize critical data.
Advanced connected worker platforms can deliver training and detailed standard operating procedures on mobile and wearable devices in a clear, visual, and engaging way that is optimized for the frontline worker. Work instruction and processes such as inspections and maintenance can include embedded micro-training and are made more effective through the use of smart logic and automations that guide and assist workers in executing their tasks.
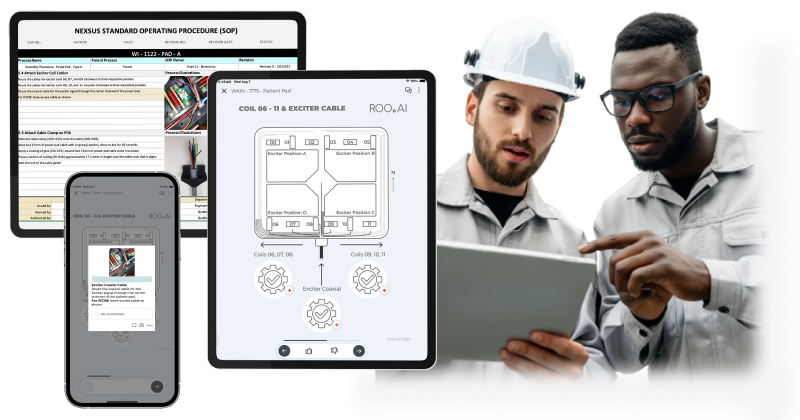
With the advent of Bots and AI, advanced connected worker platforms become powerful digital assistants for workers, providing context-relevant suggestions, summaries of prior findings, or even next steps for the operators to take based on the data being collected.
Beyond providing access to information, a connected worker platform enhances collaboration by breaking down silos between teams, ensuring workers can quickly share insights, report issues, and receive guidance — no matter where they are. This seamless integration of technology helps reduce errors, improve compliance, and accelerate decision-making on the job.
Finally, top tier connected worker platforms include flexible reporting and analytics capabilities to gain insights from activity tracking and data collection. A flexible API enables integration with core enterprise systems, MES and corporate business intelligence applications.
Case Studies – Real World Connected
Workforce Examples
1. Oil&Gas Field Service Provider Improved Return on Assets and Onboarding Process
After the pandemic, this leading OFS company had to rapidly rehire and had more workers new to oil field services in key positions than ever before. The operations team digitalized the equipment inspection, repair and chargeback process. In tandem, the training team took up the challenge of making training more valuable and effective as a mechanism to onboard quickly and upskill the workforce. The result:
-
Streamlined Equipment Turnaround
Digitalized inspections ensured consistent and accurate setup and return of equipment. -
Improved Cost Recovery
Automated generation of inspection reports with images of damage enables recovery of repair costs. -
Interactive Learning
Engaged new workers with an interactive, tailored experience boosting skills acquisition and student satisfaction. -
Instant Technical Resources
Workers can quickly reference manuals for proper procedures and safety compliance. -
In Field Training Access
Supervisors use ROO.AI on-site to provide real-time guidance and illustrate safe procedures.
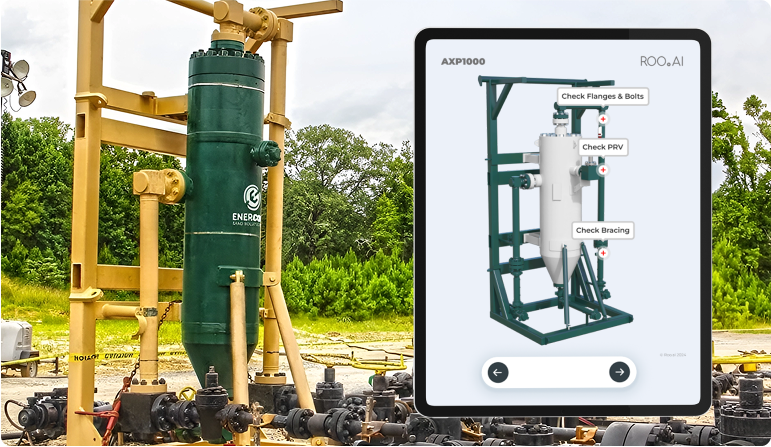
2. Fire Apparatus Manufacturer Optimizes Quality Control
The oldest continuously operating manufacturer of fire apparatus was facing challenges meeting the demand for their MTO fire apparatus. With millions of possible configurations, it was critical to spot in-process defects and resolve them quickly, but the paper-based process that was used slowed both visibility and response to issues. Implementing a connected worker solution from ROO.AI fully digitalized the quality control process from the initial build of customized stainless steel frames to final customer acceptance inspections. Benefits included:
-
Instant Visibility To Defects
Defects were documented with images and video and immediately visible to quality and production management. -
Automated Defect Data Capture
Defect reports were automated and data was categorized to drive continuous improvement efforts. -
Faster Turn Around Of Defect Resolution
Defect data was made available to production teams in real-time enabling repairs to happen faster. -
Improved Operational Visibility
Realtime dashboards provided management with visibility by department to apparatus progress. -
Automated Documentation
All inspections, defects and resolutions are automatically documented and digitally stored providing easy traceability and auditability.
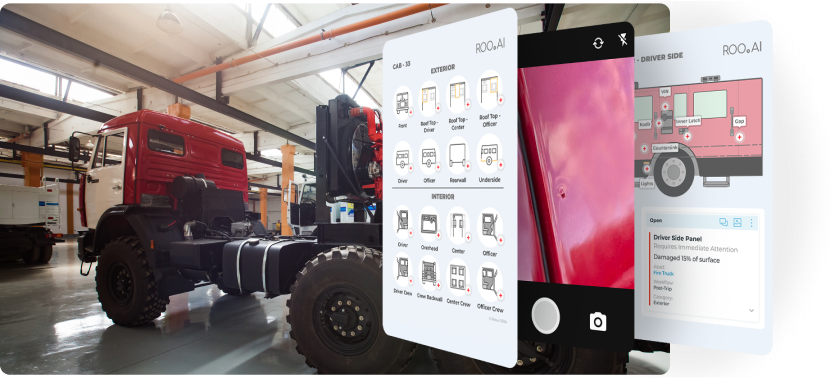
3. Logistics Provider Ensures Safety Compliance and Reduces Claims Risk
A growing specialty logistics provider found themselves at a disadvantage when dealing with damage claims and customer complaints. They also planned to expand their business into specialty foods which required strict adherence to and documentation of regulatory procedures. They implemented a connected worker platform from ROO.AI to ensure standardized loading processes, documentation of all shipments and all required inspections to help them pass regulatory audits. Benefits included:
-
Improved Customer Satisfaction
Customers reported fewer issues and loved the digital reports that accompanied shipments. -
Enhance Compliance to OSHA
Digitalized pre-operation inspections for power lift equipment were easier and faster for operators. -
Reduced Maintenance Costs
More consistent equipment inspections enabled better preventive maintenance and fewer breakdowns. -
Cut Administrative Time
Managers used ROO.AI for employee write-ups and corrective actions, reducing paperwork. -
Automated Regulatory Reporting
Digitalized inspections and safety checks reduced the effort required for regulatory audits. -
Reduced Claims
Digitalized shipment reports provided visual proof of service and saved the company enough in the first claim to pay for ROO.AI for 5 years.
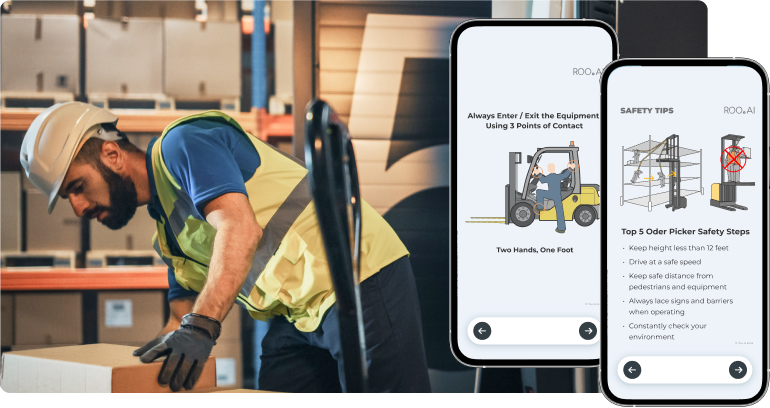
These case studies highlight how connected worker technologies drive real business outcomes across industries.
How to Choose the Right Connected Worker Solution
Before implementing a connected worker strategy, ask yourself:
What are the key pain points?
Who are you connecting?
What tasks are they performing?
What are the downstream and upstream processes?
What data do they need?
Which existing systems need integration?
What are the resource requirements?
Answering these questions will help you identify the right connected worker solution for your needs.
The Competitive Advantage of Early Adoption
Connected worker is not a future concept—it’s already transforming industries today. Companies that embrace digital assistance and connectivity on the frontline gain a competitive edge in efficiency, worker safety, and agility.
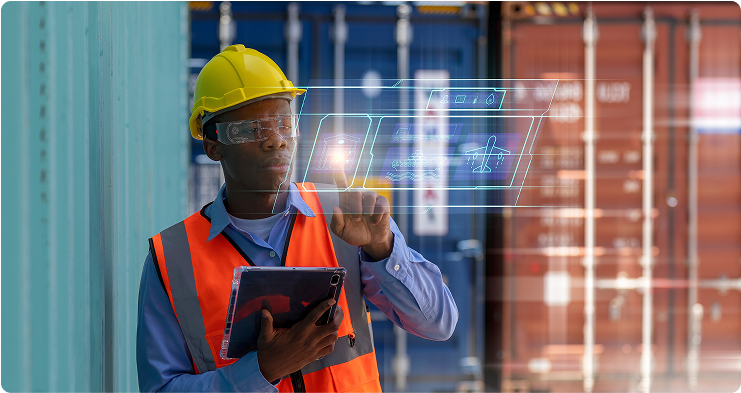
Powering Frontline Excellence with ROO.AI
ROO.AI transforms the way frontline teams work by equipping operators and field technicians with intuitive digital tools and integrated modules for inspections, work instructions, defect management, work orders, asset and parts management, vendor management and warranty management that align teams across work processes. Our connected worker platform accelerates onboarding and upskills employees faster—empowering production, quality, and maintenance teams to operate at peak performance.
With ROO.AI’s intuitive visual interface, on the spot guidance powered by smart automations, Bots and AI, and automated data collection, frontline workers receive real-time support, while businesses gain actionable insights for smarter decision-making.
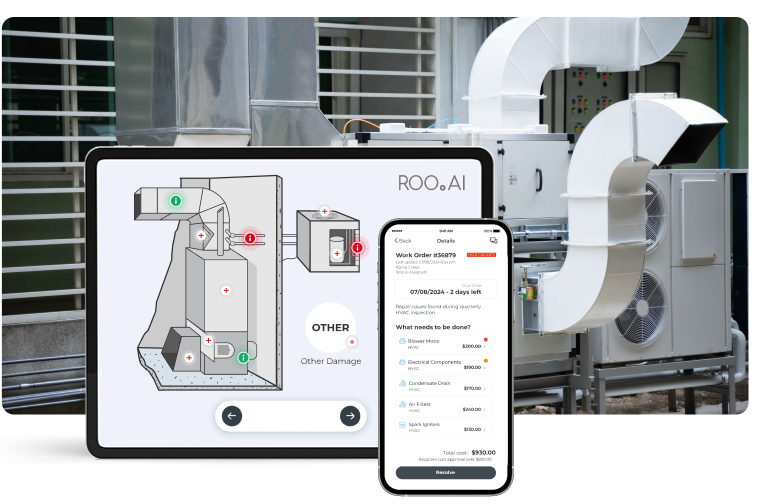
Seamless Implementation—No Coding Required
Forget complex software configurations—ROO.AI takes care of everything for you. No need to build forms or write code. Our expert team handles system setup, design, and testing, ensuring a smooth, hassle-free rollout. The ROO.AI success team also handles ongoing modifications and enhancements, allowing your resources to focus on your business.
Implementation timelines vary based on process complexity and integrations. Many businesses are up and running in as little as two weeks, with typical deployments completed in 4-6 weeks.
Dedicated Support for Lasting Success
Every customer is assigned a dedicated Customer Success Executive, ensuring you maximize the value of your investment. Our ROO.AI Concierge service also includes an implementation lead, providing continuity and in-depth knowledge of your unique operational needs.
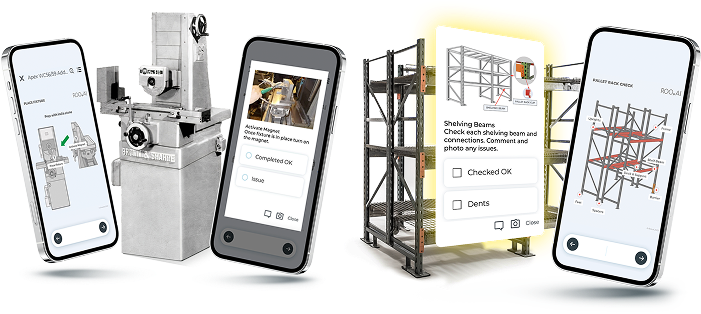