FREE WAREHOUSE
SAFETY CHECKLIST
Download our free PDF warehouse inspection form or get a live demo to discover how we incorporated this checklist into an easier, faster mobile app with visual inspection assistance.
Get Live Demo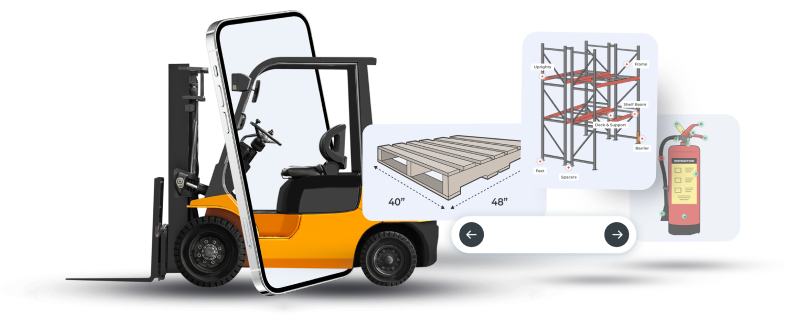
Warehouse Safety
A safe warehouse environment promotes both operational efficiency and employee well-being. Incorporating a regular inspection process and preventive measures can mitigate potential hazards in warehouse settings. This introduction to warehouse safety covers the key risks, such as forklift operations and outlines essential safety practices.
Machinery and Equipment Safety
- Regularly maintain and inspect warehouse machinery, provide thorough training to operators, and enforce the use of protective gear to prevent accidents and ensure safe equipment handling.
Preventing Common Warehouse Hazards
- Handling Materials Safely: Use proper lifting techniques and equipment to prevent strain injuries.
- Avoiding Slips, Trips, and Falls: Maintain clean, clutter-free floors and use non-slip mats in high-risk areas.
Regular Safety Training Sessions
- OSHA has established guidelines for training divided into five industry groups. Depending on the industry, the training areas include: Emergency Action, Fire Prevention, Power Platforms (Equipment), Noises Exposure, Hazardous Materials. More information can be found here.
OSHA Guidelines and Compliance
- Ensure adequate space in aisles, loading docks, and passages for safety. Implement visual alerts near dock edges. Adhere to established protocols during the refueling of gas or propane-powered forklifts. Educate employees about the risks linked to forklift operation byproducts, like carbon monoxide.
Creating a Culture of Safety
- According to OSHA, “A strong safety and health culture is the result of positive workplace attitudes – from the chief executive officer to the newest hire; involvement and buy-in of all members of the workforce; mutual, meaningful, and measurable safety and health improvement goals; and policies and procedures that serve as reference tools, rather than obscure rules.”
Record-Keeping and Documentation
- Depending on the industry, companies with over 10 employees are expected to maintain records to validate their inspections and hazard mitigation processes and corrective actions, and are required to post annual summaries of work related accidents and injuries. This documentation is required to be maintained for a period of five years.
Fire Safety Protocols
- Conduct frequent drills to ensure staff are well-versed in evacuation procedures.
- Position extinguishers throughout the warehouse and ensure they are easily accessible.
- Maintain unobstructed pathways to exits, clearly marked with signage.
- Regularly inspect electrical systems to identify and rectify potential fire hazards.
- Install and maintain smoke detectors and fire alarms to provide early warning.
- Develop and communicate a clear plan detailing steps to take in case of a fire.
Essential Safety Equipment in Warehouses
- Safety Helmets: Protect against head injuries from falling objects or collisions.
- High-Visibility Vests: Ensure workers are easily seen, reducing accident risk.
- Steel-Toed Boots: Guard feet against heavy object impacts.
- Protective Gloves: Shield hands during handling of hazardous materials.
- Respirators or Masks: Required in environments with dust, fumes, or harmful gases.
- Safety Glasses: Shield eyes from flying debris and hazardous liquids.
Machinery and Equipment Safety
Preventing Common Warehouse Hazards
Regular Safety Training Sessions
OSHA Guidelines and Compliance
Creating a Culture of Safety
Record-Keeping and Documentation
Fire Safety Protocols
Essential Safety Equipment in Warehouses
Core Elements of a Safety Checklist
Stay Compliant and Save Time - Go Digital
ROO.AI Improving Warehouse Safety
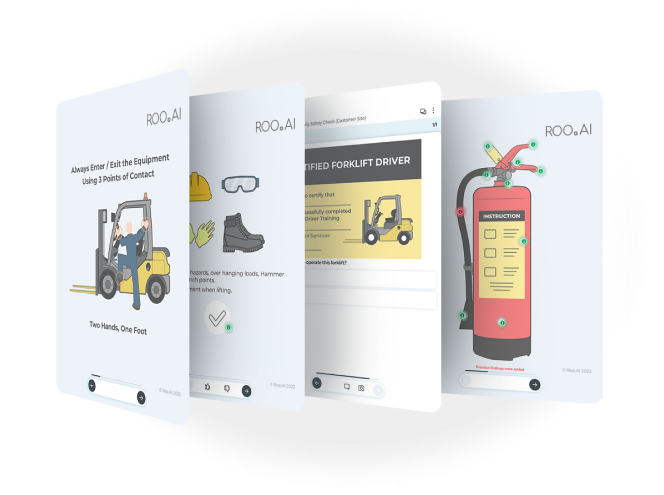
The Power of Visual Instruction
Guide workers through inspections, receiving and loading processes with quick, easy visuals to ensure the job is done correctly every time including image verification and worker signatures.
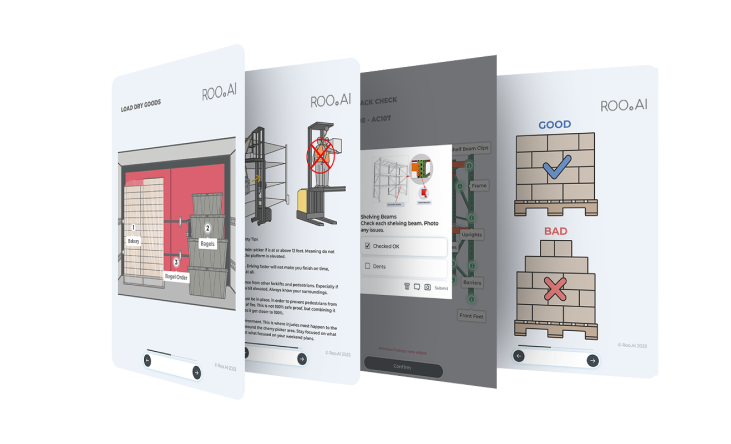
Encouraging Safety Mindfulness
Accelerate onboarding and engage your employees with easier more effective safety training. Equip new team members with the essential skills and standard procedures through clear visual guidance. Provide on-the-spot training and integrate safety into standard operating procedures
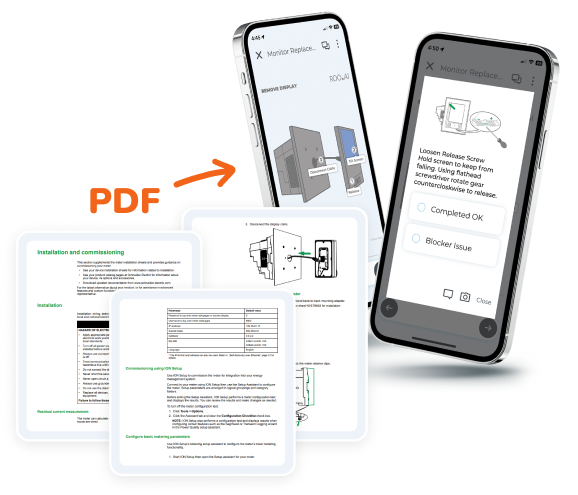
The Role of AI
Transform your traditional documents into dynamic digital workflows with ROO.AI. Effortlessly convert forms, checklists, PDFs, and spreadsheets into optimized, user-friendly digital formats. Plus, our AI technology can turn any process video into detailed digital instructions and inspections, streamlining your workflow like never before.